Structural Mechanics and Materials Behavior
(text and background only visible when logged in)
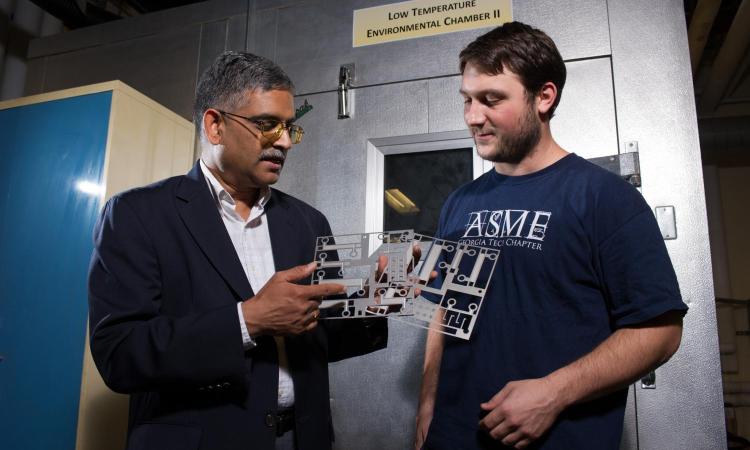
Focus
This research group seeks to understand and predict the material and related structure behavior in environments and in applications that are unique to aerospace engineering. Specific areas of inquiry include computational mechanics, composite structures, fracture and fatigue, damage tolerance and failure prediction, experimental mechanics, thermal and environmental effects and non-destructive evaluation, structural stability (buckling/postbuckling), adaptive structures, structural health monitoring, and system identification.
The group actively addresses many longstanding research issues, including conventional metallic aero-structures, such as life extension in aging aircraft and proper methods of vibration control. As standards for safety, performance, and lifecycle costs continually evolve, SMM is committed to evaluating and incorporating new, advanced materials such as composites with toughened thermosetting matrices, thermoplastic composites, and metal-matrix or ceramic-matrix composites. The team has focused on damage tolerance/fatigue/fracture; airworthiness; impact-resistance; efficient and accurate computation tools (finite elements, etc.); modeling of the mechanics of manufacturing; new structural design concepts (ply drop-off, sandwich construction, elastic tailoring); anisotropic elasticity and plate/shell higher-order or asymptotic theories; and diagnostic methods including C-scan, acoustic emission, and X-ray.
(text and background only visible when logged in)
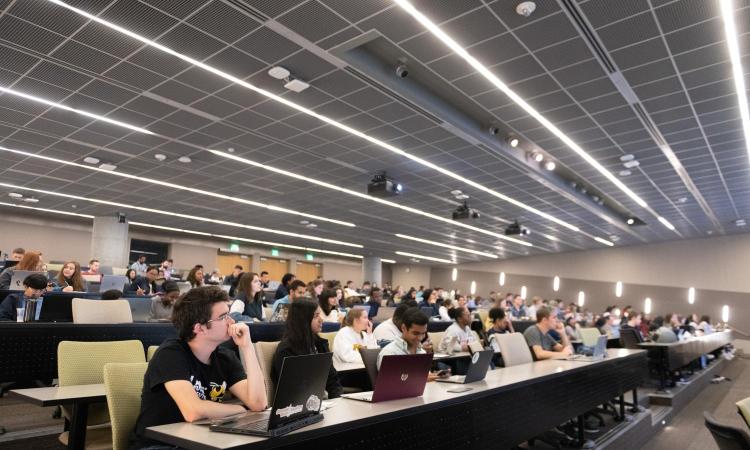
Impact
The constant need for safer, lighter, better-performing aerospace vehicle applications has always been the goal of this research. The SMM group supports research that investigates the many structural parts of commercial and military airplanes and space vehicles now being made of new, advanced materials. With the support of numerous public and private sponsors - ONR, ARO, AFOSR, and VLRCOE, to name a few – graduate SMM research teams take on a variety of challenges in contemporary aero structure and materials: primary carbon-epoxy structures in the vertical tails of the Airbus A300-340 series; the Boeing 777 transports; the B-2 military aircraft’s wings and fuselages; the Comanche helicopter, and various components of the space shuttle. The group analyzes structural design criteria for aero-structures, including damage tolerance requirements that are specific to their ability to operate safely with initial defects or in-plane damage. The SMM group seeks to identify and mitigate the effects of typical defects such as porosity, delamination, lack of bond between co-cured parts, and wrinkles in fibers. It also explores how low-velocity impacts cause low-level ‘invisible’ damage while high-velocity impacts (e.g, from the failure of rotating machinery or ballistic damage) can immediately affect airworthiness. New concepts in design, such as sandwich or hybrid material construction, new manufacturing techniques and new material developments are studied to determine whether they introduce undesirable residual stresses and deformations or require new methods of analysis and testing.
(text and background only visible when logged in)
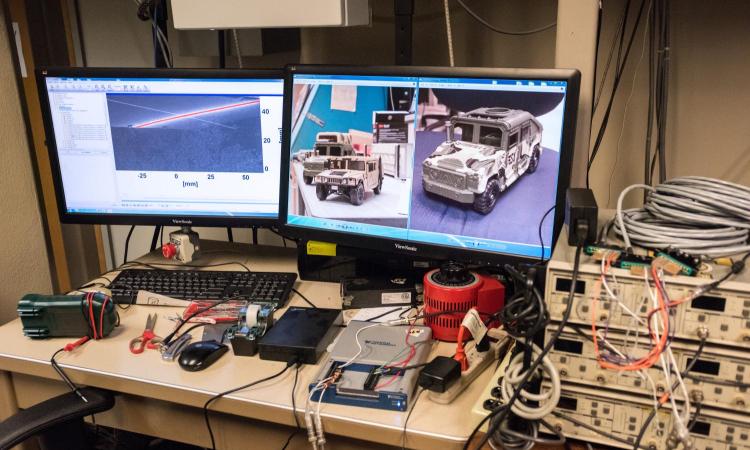
Facilities
Located in the basement of the Knight Building, the GT-AE Structures Laboratory is well-equipped with advanced test frames, optical equipment for the remote monitoring of cracks, and a variety of non-destructive testing equipment and related computerized data acquisition systems. In the Weber Building are labs that feature a filament winder, an autoclave for the manufacturing of composite specimens, a strain-gauge, and an optical deformation system, and WHAT? Dedicated computer workstations WHERE can be used for large-scale computational research and stress analysis.
(text and background only visible when logged in)
Academic Resources
The SMM group is composed of tenure-track professors, research engineers, and graduate students and post-doctoral fellows. To find out more about the focus and impact of our work, we encourage you to visit the profiles of the SMM faculty, the SMM lab websites, and the lab sites for the Georgia Tech multidisciplinary research centers associated with this discipline.
(text and background only visible when logged in)