AE student designs a small test engine during NASA internship that’s helping engineers explore new, more powerful rocket designs.
Dalton Luedke has created a model engine that’s helping NASA lay the foundation for deep space exploration to the moon and Mars.
During a summer internship at the space agency, Luedke worked with a team exploring new rocket designs that are more powerful and weigh less. But his contribution — “sizable,” in NASA’s own words — is small enough to hold in your hand.
Luedke is a third-year aerospace engineering student, and he’s always had a connection to aviation. His father worked as an air traffic controller in the U.S. Air Force and now develops and sells air management software to air traffic control towers. Many of his friends are studying aerospace engineering.
Luedke always had a knack for science and math. Growing up in Woodstock, Georgia, he knew Georgia Tech would be the perfect place to explore those interests.
Luedke quickly found his place on campus at the Yang Aero Maker Space (AMS), where he worked as a mentor at first before moving into an officer position. He said all those hours working in the AMS first exposed him to manufacturing processes and gave him the opportunity to delve deeply into hands-on projects.
“Working at the AMS gave me exposure to a variety of machining and manufacturing processes. Most notably, we do a lot of 3D printing within the maker space specifically for aerospace labs. This exposure allowed me to develop a large knowledge base related to additive manufacturing for aerospace applications,” Luedke said.
“Importantly, I learned a lot about design for manufacturing as it pertains to additive manufacturing since part of my job at the AMS is to communicate with labs the best way to design and manufacture different parts,” he continued. “This helped me in my work at NASA as I had to design my engine for additive manufacturing.”
Luedke was looking for a summer internship when one of his instructors sent out an announcement about NASA’s Pathways Internship Program. Describing it as one of the “end-all, be-alls of working in aerospace,” Luedke knew he couldn’t pass up the opportunity of working at NASA. So, he applied.
Luedke was selected for the program, and he joined the advanced liquid propulsion team at NASA’s Marshall Space Flight Center. The team there was working on a rotating detonation rocket engine (RDRE) in hopes of changing how propulsion systems are designed for deep-space travel. Rotating detonation rocket engine designs can produce more power while weighing less than today’s most common propulsion systems. It was on this project that Luedke made his mark.
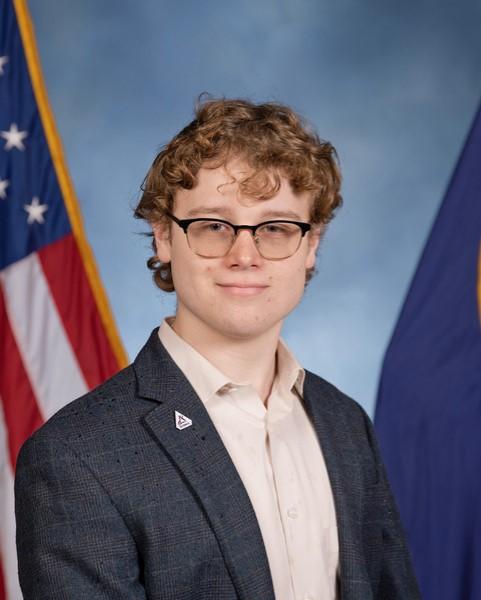
Dalton Luedke
(text and background only visible when logged in)
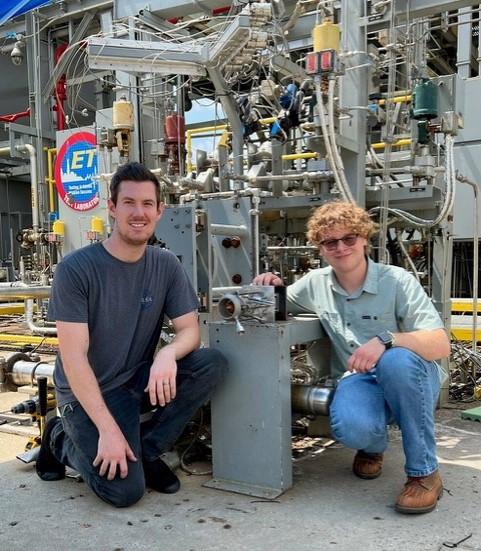
Thomas Teasley, left, a liquid propulsion engineer at NASA’s Marshall Space Flight Center, and Dalton Luedke, right, NASA Marshall Intern.
Originally tasked with designing a small-scale RDRE with a quartz combustion chamber so the team could observe the combustion, Luedke realized the small model had much larger possibilities.
“I ended up designing the subscale RDRE to be modular so that you can swap out components very easily,” Luedke said. “We can test different combustion chamber configurations, different injectors, different nozzles, different inner bodies, all sorts of different things.”
Luedke’s innovative approach streamlined testing the RDRE, allowing his team at NASA to successfully test 12 unique configurations on the model. Luedke and the team believe these tests indicate the RDRE has potential to change future rocket design approaches and make space travel far more efficient.
“It is basically unheard of for a student engineer to go and do the development on a combustor all by themselves,” said Tom Teasley, a liquid propulsion engineer at Marshall who worked with Luedke on the engine. “Much less the fact that he was able to do the development, the post-processing, and then fire it before the completion of his internship.”
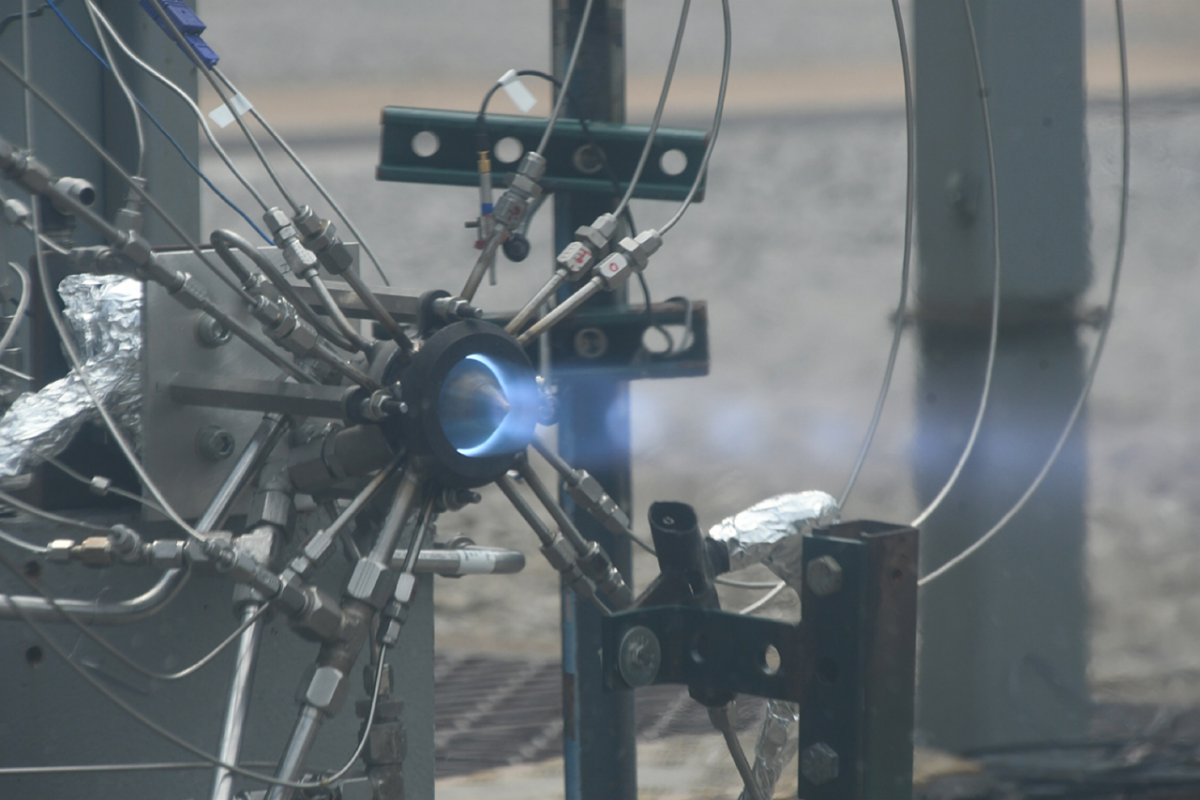
Experimental test of Luedke's small-scale rotating detonation rocket engine.
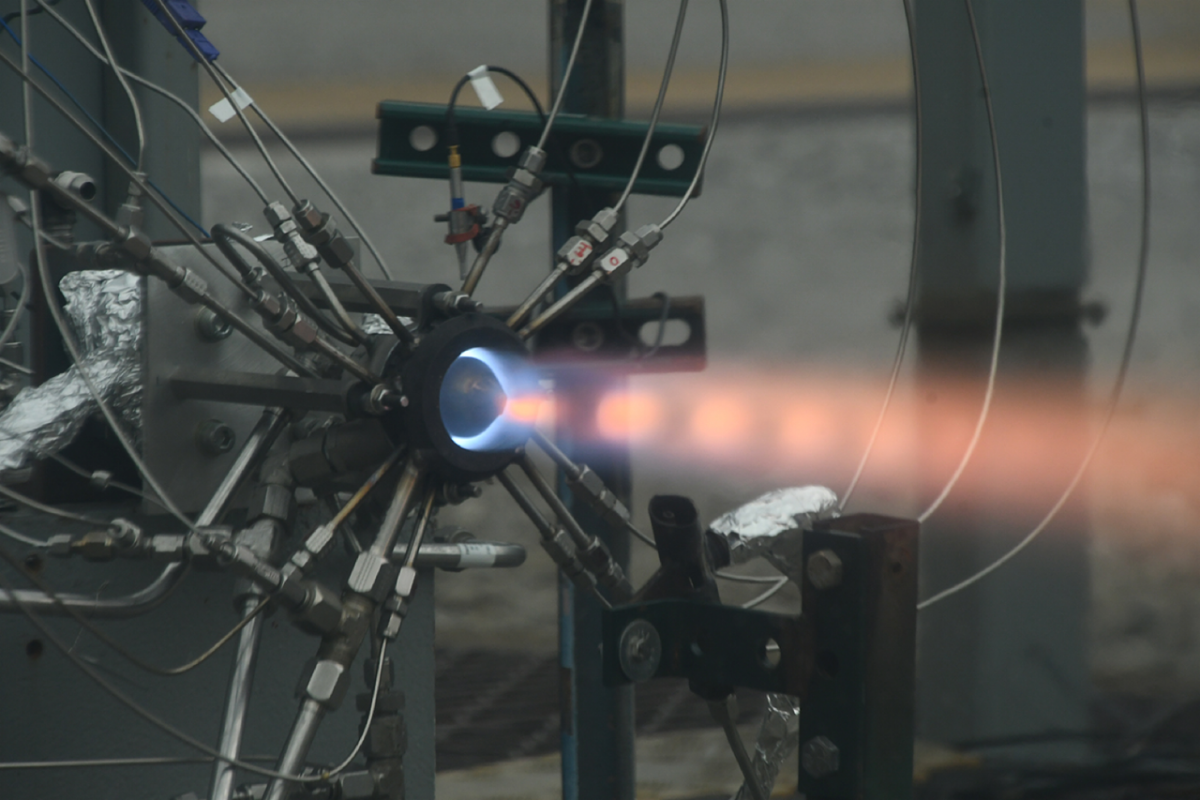
Experimental test of Luedke's small-scale rotating detonation rocket engine.
Although his internship officially ended in August, Luedke continues to be involved with the project.
“I'm in the process of doing data reduction, where I am going to be the first author on a couple papers on [the project],” Luedke said. “Following the success of these tests, the propulsion department at Marshall as well as commercial space companies are very interested in continuing the research.”
In early 2024, Luedke will work with his NASA team on several new tests for the project.
“We’re going to be testing combustion chamber length, and then we have another test campaign, hopefully next summer, to test injector design. I will be doing all of the design and test planning on that and then helping write the journal papers after,” Luedke said.
The importance of Luedke’s design is the size; it is more affordable to manufacture, manage, alter and test than a full-scale RDRE, yet it functions the same. As the team moves toward flight demonstrations of the RDRE, Luedke said his subscale model will be key to improving the engine’s function and perfecting the system at full size.
Luedke said the project revealed a new, unexpected passion and direction for his career.
“I thought I wanted to go into [a broad spectrum of] structures and now I know that's not true,” Luedke said.
Now his attention is focused on another summer working with the liquid propulsion team and eventually securing a full-time position at NASA. He’s all-in on propulsion research and helping create innovative approaches to space travel — and he’s focusing his courses on that ambition.
“I spend more time in classes related to propulsion, thermodynamics, and combustion. This [opportunity] has allowed me to direct my education more toward where I want to go,” he said.
(text and background only visible when logged in)